Food and Beverage
As new food and beverage processing equipment with complex and sensitive electrical systems, controls and automation continues to replace older generation equipment, MRO expenses are rising with increasing maintenance time, technical support and power costs. Food and beverage processing plants require a high sustainability level from their electrical systems, because shutdowns can cost from minutes’ to days’ worth of production if a batch must be scrapped.
Plant capital expenditures are also increasing due to existing capacity constraints. They’re being justified with process and packaging improvements using sanitary plant designs that reduce product contamination and facility cleaning times, while increasing operational equipment effectiveness (OEE), revenues and plant sustainability. To increase productivity and food safety, processing equipment must be designed with geometries that quickly shed contaminants and allow easy cleaning, often in harsh processing environments.
Food and beverage facility cleaning and sanitation crews often use high-pressure hosedown cleaning equipment with high-temperature caustic chemical solutions that shorten the life of the facility and equipment. This is being offset by the use of corrosion-resistant materials such as stainless steel, aluminum, specialty alloys, high-tech non-metallics and coated materials. Food and beverage plants often have extreme temperature ranges due to processing requirements. Thermal cycling issues from ovens directly in line with flash freezers can cause reliability issues in processing areas.
Shortened product-development cycles, smaller batch sizes, fast expiration dates and more frequent product-type changeovers require adding new automation technologies for better processing flexibility, keeping production costs down and getting products to customers quickly. With nearly 90% of food and beverage plants having fewer than 100 employees
and many having been small, family-run businesses acquired by larger companies, the need for electrical system standardization has become more critical.
Thomas & Betts provides food and beverage
electrical system solutions that:
– Increase your overall equipment effectiveness
– Extend the life of your electrical system by up to 300%
– Decrease electrical system changeover and downtimes by 40–50%
– Increase food safety, reduce product contamination and provide a safe workplace for your employees
These solutions enable food and beverage processors to increase revenue, plant sustainability, food safety and brand equity.
For over a century, Thomas & Betts has provided food and beverage companies with electrical system solutions to help protect their people, assets, brands and customers, while increasing food safety, plant sustainability and revenues.
Ocal® – better by design
Ocal® PVC-coated conduit and fittings represent a complete corrosion protection package for your entire conduit system. This extensive product line includes an extensive number of items in stock along with corrosion-resistant supports and patching compounds. With Ocal® PVC-coated conduit and fittings, you get corrosion protection that will help extend the life of your electrical raceway system for years and years. Complete corrosion protection solutions:
– UL® Listed with both the zinc coating and the PVC coating investigated and listed per UL6.
– Industry-leading thread protection through a hotdipped galvanizing process, and industry-leading UL® Listed Type 4X PVC-coated conduit bodies.
– A full undisturbed zinc coating under the PVC coating, meeting the requirement of NEMA RN-1 regarding the restriction of harmed or eroded zinc coating over the conduit.
– Meets the requirements of NEMA RN-1* without exception.
– UL® Listed including UV resistance testing.
– “Double-Coat” coated fittings, enhancing corrosion protection by applying the coating to the interior and exterior of the fittings before PVC coating.
– Custom colors.
PMA Conduit – Flexibility and cleanability for the food and beverage industry
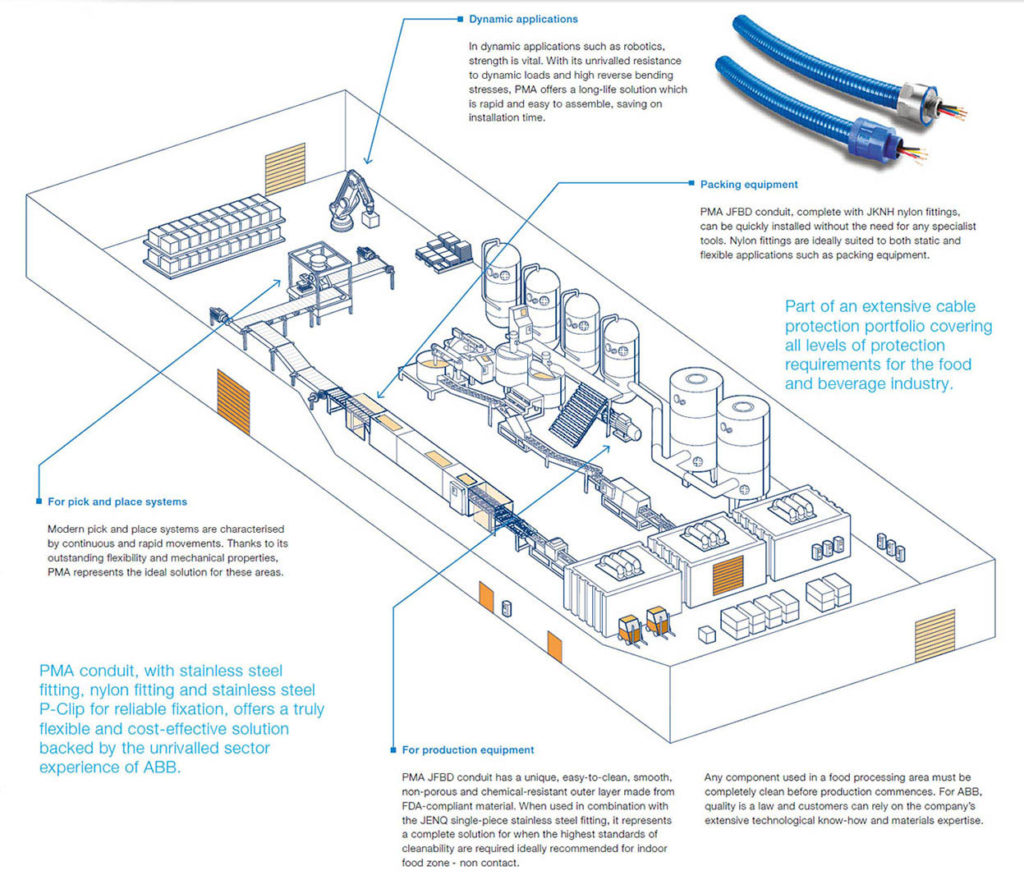
ABB’s PMA conduit protects vital cables against mechanical and other environmental factors – an especially critical function in sectors with strict requirements on hygiene and cleanliness.
ABB developed the JFBD nylon conduit to feature a corrugated design especially for the food and beverage industry, the result of intensive effort by ABB’s dedicated research & development team.
To meet ever more stringent demands for rapid and effective washdown, the new JFBD conduit incorporates for the first time an over extruded non-porous smooth jacket, delivering further enhanced cleanability alongside unrivaled resistance to aggressive chemicals to ECOLAB standards.
The IP69-rated PMA cable protection range for the food and beverage industry offers a choice of two high specification fittings. The JKNH nylon fitting is made from FDA-compliant material, and offers both excellent chemical resistance and quick installation, without the need for tools. The JENQ single-piece fitting is made from 316L stainless steel and is ideally suited to areas with the highest hygienic demands.
The JFBD conduit, with either the JENQ stainless steel or JKNH nylon fitting, offers a truly flexible and cost-effective solution for the food and beverage industry, backed by the unrivaled sector experience of ABB.
T&B Liquidtight fittings – Engineered to
perform in the toughest environments

Available in Steel, Stainless Steel, Aluminum and High Temperature.
No Moisture Pooling: The distinctive pumpkin-like appearance and unique gland nut on T&B Liquidtight fittings deflects water away from the connector and prevents pooling.
Double-Beveled Sealing: T&B Liquidtight’s unique sealing mechanisms, made from high-temperature rated thermoplastic in a distinctive blue coloring, can’t be installed backwards — error-free installation designed in.
Infinitely Adjustable: Save time and money with revolver grounding fittings that use an infinitely adjustable rotating ground lug.